Winding Consulting

The manufacturing operation was experiencing wound roll quality issues on film/film laminated products slit and rewound on a REM slitter/rewinder. The problem was described as rolls blowing out and is mostly an issue after winding although there have been problems on 3000 foot 5 to 6 inch wide slits during winding. The client was not sure whether the problem was due to circumferential slip (cinching) during winding or excessive conveyance and handling forces.
Test System for Filtration Company

Donaldson Company Inc. provides industrial filtration solutions to a variety of markets. To quantify the performance of the company’s filters, they are tested to the American Society of Heating, Refrigerating and Air Conditioning Engineers (ASHRAE) specifications to determine how efficient the filter is at removing particles of various sizes. To further stress the filters during testing, the environmental conditions need to be widely varied from 50 to 90 °F, 20 to 98% relative humidity, and 600 to 3000 cfm airflow. The previous test bench used by Donaldson Company was undersized and not capable of achieving the high or low extremes of many of the test specification requirements. Additionally, as the ASHRAE test standard evolved over time, the old system approached its usable life span.
Upgrade of 750 Gallon Glass-Lined Reactor
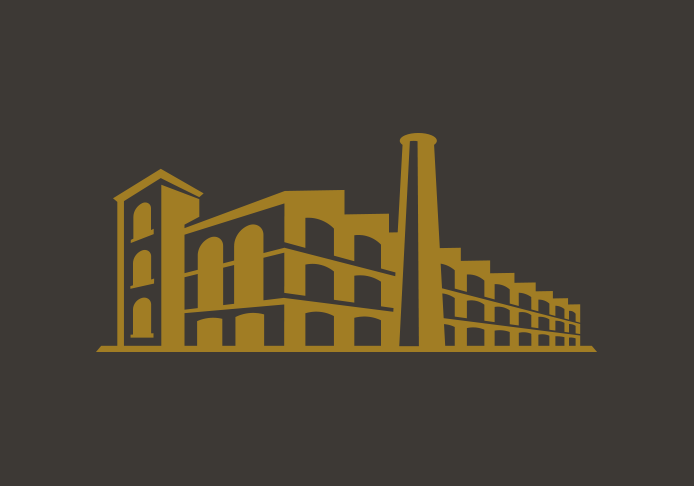
The Synthetic Chemicals Division at Building 304 in EBP had a 750 gallon glass-lined reactor, Vessel #301, that was in need of a major controls and piping upgrade to meet current division controls design by replacing obsolete mechanical and electrical components, as well as meet NYS MON/MACT regulations (NYS pollutant monitoring & capture control technology). This vessel was operating with obsolete pneumatic controls from the 1970’s, had numerous maintenance issues where spare parts were very difficult to replace, and the overall system was in need of a complete electronic/controls upgrade.
Scalable Lithium Battery Production and Assembly System
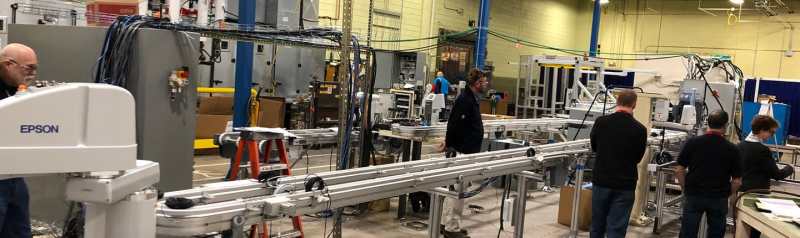
A battery manufacturer wanted to increase productivity and total product throughput on a 24-hour cycle using robot technology and other automated peripheral devices.
Re:Build Optimation was approached by a global manufacturer of specialty battery power sources, renowned primarily in defense, medical, safety, and industrial radio advanced RF communications markets. The client aimed to seize an opportunity to gain market share, revenue, and greater profitability through the introduction of advanced automated assembly capabilities. Prospective new market opportunities in wireless security and home automation meant a potentially near-immediate and explosive opportunity lay before them, if they acted quickly and effectively.
The system was to be built for their lithium products line and tailored to these market needs for optimal results. After surveying commercially available subsystems for production, the client settled on a variety of custom-designed stations to be integrated by Re:Build Optimation. The operation would be based in the company’s American manufacturing center.
Re:Build Optimation and the client specified and coordinated a backbone of custom material handling. It tied together various work-centers of existing client equipment and new custom systems. Re:Build Optimation devised an architecture that met the initial production capacity targets and could expand to deliver more than triple that amount with only small capital upgrades required as demand grew.
Retrofitted Solvent Coater

New College Institute wanted to train the local workforce in Martinsville, VA. The local economy was primarily textile and furniture manufacturing related, with limited technical positions. Two local film manufacturers, Commonwealth and CP Films, were struggling to have enough qualified resources for their facilities. New College Institute approached Ralph Schultz of Commonwealth to tackle the problem. They determined that a machine was needed to demonstrate the principles of coating and web conveyance (both essential processes in film making), in addition to a classroom setting to teach the principles. Other companies offered solutions that New College Institute couldn’t afford. Schultz then brought in Commonwealth’s longtime supplier, Re:Build Optimation. Re:Build Optimation’s team was able to offer a creative solution that met New College Institute’s budget constraints.
Production Expansion and Solvent Recovery

American Aerogel, a company developing and manufacturing proprietary aerogel insulation products, had been growing rapidly and needed to expand its production capabilities.
Because demand for its product was so high, American Aerogel’s 24/7 operation required new equipment with process improvements to increase production and improve efficiencies.
Because American Aerogel’s products are made with a proprietary one-of-a-kind aerogel called Aerocore, maintaining confidentiality of the products’ chemical makeup and patented manufacturing processes was/is of the utmost importance. Re:Build Optimation continues to honor this confidentiality.
Pilot Plant Expansion
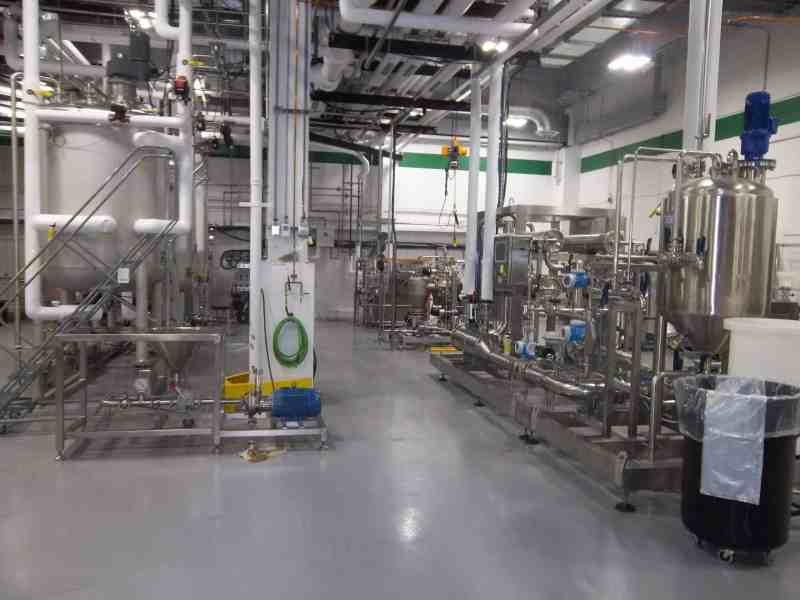
Greenlight’s Pilot Plant Expansion brought a previously installed fermenter and reactor capacity online with supporting downstream processing capabilities, product formulation, and a product packaging line to support precommercial and commercial product volumes of our first-to-the-world RNA based solutions.
Peanut Butter Plant Expansion

A metal parts manufacturing company required an automatic washing machine that would cut down on manual operation and improve its bottom line. Re:Build Optimation used its material handling and automation expertise to design a machine that would queue, load, unload and sort parts as one automated process. Re:Build Optimation then fabricated and assembled the 68-foot-long machine that met the company’s goal of a cost-effective and efficient washing procedure. The machine was solely produced by Re:Build Optimation from concept to completion, including the electrical, mechanical, material handling, process engineering, design, fabrication and assembly of each sub-system. The new washer has the room to queue up to five incoming kettles and index kettles into an automatic kettle unloader that will transfer the parts from the kettles into washer baskets. The operator delivering the kettle will make push button selections to indicate the product type tote bin and the wash cycle treatment. A washer in-feed conveyor will convey and transfer the loaded baskets into the washer system conveyor, which will take the parts through its cycle. An out-feed conveyor will receive the washed part baskets as they exit the washer and transfer the basket into a basket shuttle dumper, which will then dump the parts from the basket into the desired tote bin. The empty basket then goes back to a return conveyor for queue-up, and the process starts again.
Machine Design/Build – Parts Washer

A metal parts manufacturing company required an automatic washing machine that would cut down on manual operation and improve its bottom line. Re:Build Optimation used its material handling and automation expertise to design a machine that would queue, load, unload and sort parts as one automated process. Re:Build Optimation then fabricated and assembled the 68-foot-long machine that met the company’s goal of a cost-effective and efficient washing procedure. The machine was solely produced by Re:Build Optimation from concept to completion, including the electrical, mechanical, material handling, process engineering, design, fabrication and assembly of each sub-system. The new washer has the room to queue up to five incoming kettles and index kettles into an automatic kettle unloader that will transfer the parts from the kettles into washer baskets. The operator delivering the kettle will make push button selections to indicate the product type tote bin and the wash cycle treatment. A washer in-feed conveyor will convey and transfer the loaded baskets into the washer system conveyor, which will take the parts through its cycle. An out-feed conveyor will receive the washed part baskets as they exit the washer and transfer the basket into a basket shuttle dumper, which will then dump the parts from the basket into the desired tote bin. The empty basket then goes back to a return conveyor for queue-up, and the process starts again.
New Milk Replacer Production Facility

Grober Nutrition is in the dairy industry for animal food products in facilities built to human food standards, which is unique to the Northeast. Grober’s product is a powdered formula that is used as a milk replacer for young animals. Surplus Whey from a Skim Milk manufacturer is readily available as a supply component for the formula. The process included evaporating whey to a specific concentration, which was then used as an ingredient in producing a slurry which then fed a large dryer. The company needed a turnkey supplier for support of their new 60,000-sq-ft, state-of-the-art facility in Auburn, NY to produce the formula.